Le filetage au tour, permet de réaliser des vis pour lesquelles nous n’aurions pas de filières ou de tarauds adaptés. Il peut aussi être utilisé lorsque l’on veut une vis de grande précision.
Présentation
Pour réaliser cela, vous avez besoin d’un système de filetage avec une vis mère qui entraine le burin de filetage. Il existe plusieurs systèmes différents. Sur certain tour c’est le chariot du tour qui se déplace. Dans ce cas, la vis mère peut-être celle du chariot supérieur ou petit chariot. Dans d’autre cas, c’est le trainard qui est relié à la vis mère.
Un autre système de filetage au tour existe, comme le mien par exemple qui comporte une patronne (vis mère) et un peigne qui entraine un chariot spécial pour le filetage. Ce système se retrouve principalement sur les tours Schaublin 102.
Dans tous les cas, vous aurez encore besoin d’un train d’engrenage qui lie la broche du tour et la vis mère. On calculera ce train en fonction du pas que l’on veut réaliser et du sens de filetage (gauche ou droite).
Cette opération peut paraître compliquée à calculer, mais en fait ce n’est pas si difficile que cela. Sans entrer dans un détail mathématique compliqué, je vais vous montrer comment on fait. Ensuite on réalisera aussi en même temps une pièce filetée.
Calcul du rapport de pas
Pour commencer un filetage au tour, il faut avant toute chose connaitre le pas de la vis qu’on veut réaliser et le mettre en fraction (tuto sur les fractions ici). On appellera ce pas P1.
Exemples :
si la vis à réaliser a un pas de
mm alors : P1 sera
Si la vis à réaliser a un pas de
mm, alors : P1 sera
Si la vis à réaliser a un pas de
mm, alors : Pour mettre en fraction une valeur périodique, c’est très simple. On prend tous les chiffres de la période que l’on met en haut de la fraction (dividende) et on met en bas de la fraction (diviseur) autant de 9 qu’il y a de chiffre dans la période donc pour nous :
P1 sera
. En mettant au même dénominateur commun on a :
qui s’écrit aussi
.
Ensuite il faut connaitre le pas de la vis mère (celle qui entraine le burin) qu’on appellera P2. Selon les systèmes, on dispose de plusieurs vis mères avec des pas différents.
La formule à appliquer est :
. C’est en fait le rapport qu’il y a entre le nombre de tour de la broche et le nombre de tour de la vis mère. Donc si j’ai une vis mère avec un pas de 2 mm, on aura selon mes exemples précédents pour :
P1 =
mm ==>
tour de vis mère pour un tour de broche.
P1 =
mm ==>
tour de vis mère pour un tour de broche.
P1 =
mm ==>
tour de vis mère pour un tour de broche.
Choix des engrenages
Il reste maintenant à déterminer le rapport d’engrenage qui correspond à cette fraction. Vous trouverez ici, un tuto sur le calcul des rapports d’engrenage. Je ne vais donc pas m’attarder à cela ici. Toutefois, il est important avant de partir dans le rapport d’engrenage, de connaitre dans quel sens va tourner votre pièce et votre vis mère. Si votre filetage est dans le même sens que la vis mère (droite ou gauche), alors la vis mère tournera dans le même sens que votre pièce, sinon elle tournera dans l’autre sens.
Si vous disposez de plusieurs vis mères, il vous faudra réaliser toutes ces opérations pour chaque vis mère que vous avez. Si aucune solution n’est possible, alors il faut acheter ou fabriquer d’autres engrenages.
Une dernière petite chose importante avant de vous lancer. Si vous disposez d’un système débrayable comme le mien, il faudra faire attention de ne surtout pas débrayer entre les passes, lorsque le pas que vous réalisez n’est pas un diviseur du pas de la vis mère. En d’autre terme, si vous divisez le pas de la vis mère, par le pas à fileter et que le résultat n’est pas un nombre entier, alors ne pas débrayer, sinon on risque de ne pas se retrouver dans le bon pas. En pratique si vous avez plusieurs vis mère et que votre système est débrayable, vous choisirez de préférence, une vis mère qui est un multiple du pas à fileter. Si vous ne débrayez pas, il faudra absolument dégager le burin lors du retour, afin de permettre le rattrapage du jeu qu’il y a dans la vis et les engrenages.
Montage des roues
Voilà, maintenant passons à la pratique. Je dois réaliser une vis M33 x 2.00. J’ai une vis mère avec un pas de 2mm. Je vais donc partir sur mon premier exemple pour le montage des roues.
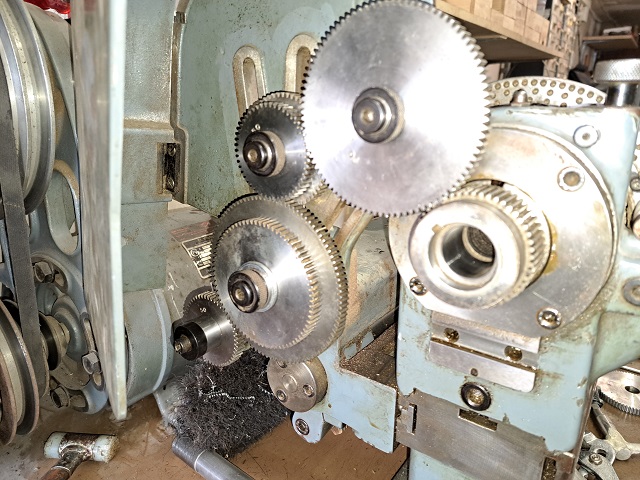
Sur mon système, la première roue solidaire de la broche comporte 50 dents. Donc j’ai monté la dernière roue (celle solidaire de la vis mère), une roue de 50 dents. Entre deux, c’est uniquement de la transmission et inversion de sens. On voit que j’ai aussi utilisé deux roues qui n’engrènent avec rien. Elles sont là uniquement comme entretoises.
Montage du système de filetage
Avant de fileter, il est nécessaire de connaître l’angle d’inclinaison de l’hélice du filetage, afin d’incliner notre burin de la bonne valeur. Lorsque l’on dessine un profil de pas, il est en fait en coupe perpendiculaire au filet. Donc notre burin qui a la même forme que le profil dessiné, doit être incliné pour respecter ce profil. Vous trouverez la formule pour calculer cet angle dans le pdf suivant, ainsi que la formule pour calculer la profondeur du pas. Ces formules sont pour un pas métrique.
La mesure sur pige (M) que vous avez trouvée dans le pdf, peut vous être utile, si vous réalisez une vis et que vous n’avez pas l’écrou pour tester votre filetage. Vous pouvez prendre un morceau de matière de votre stock, que vous mesurez précisément et vous faite le calcul avec ce diamètre de piges. Si vous le faites comme cela, avec des piges à tenir dans la main, vous avez meilleures temps d’en prendre que deux.
Je vais maintenant monter la vis mère et préparer le chariot de filetage. Dans la vidéo qui suit, vous verrez le système par peigne et patronne qui est présent sur bons nombres de tours Schaublin 102.
Passons maintenant aux derniers réglages.
On est maintenant prêt à fileter. Je mets personnellement toujours, quel que soit le diamètre, la plus petite vitesse de rotation et j’adapte mes profondeurs de passes en fonction.
Réalisation
En résumer, ce qu’il faut comprendre du filetage au tour, c’est que ça dépanne très bien, mais que c’est relativement long à mettre en place. En tout cas pour le système par peigne et patronne. Par contre ce système à l’avantage d’avoir plusieurs vis mères interchangeables. Tous les systèmes nous permettent de réaliser n’importe quel pas, pour autant que l’on dispose des bonnes roues dentées.
J’espère que cela vous a permit d’y voir un peu plus claire sur le filetage au tour. N’hésitez pas à laisser vos commentaires en dessous.
A bientôt
PAM
Retrouvez également toutes mes vidéos sur ma chaine YouTube.